Recognizing Porosity in Welding: Checking Out Reasons, Effects, and Avoidance Methods
As specialists in the welding market are well mindful, recognizing the causes, effects, and prevention techniques connected to porosity is crucial for achieving robust and trustworthy welds. By diving into the origin creates of porosity, examining its harmful impacts on weld quality, and checking out effective prevention methods, welders can boost their understanding and skills to produce top notch welds continually.
Typical Sources Of Porosity
Contamination, in the form of dirt, grease, or corrosion on the welding surface, produces gas pockets when heated, leading to porosity in the weld. Improper shielding happens when the shielding gas, generally utilized in procedures like MIG and TIG welding, is unable to fully shield the molten weld pool from responding with the bordering air, resulting in gas entrapment and subsequent porosity. In addition, inadequate gas protection, typically due to wrong circulation prices or nozzle positioning, can leave parts of the weld unsafe, enabling porosity to form.
Results on Weld High Quality
The presence of porosity in a weld can significantly compromise the total quality and stability of the welded joint. Porosity within a weld creates gaps or tooth cavities that compromise the framework, making it extra susceptible to splitting, deterioration, and mechanical failure.
In addition, porosity can prevent the effectiveness of non-destructive testing (NDT) methods, making it testing to spot other issues or gaps within the weld. This can lead to significant security problems, particularly in critical applications where the structural honesty of the welded components is extremely important.

Prevention Techniques Review
Provided the destructive influence of porosity on weld top quality, reliable prevention techniques are essential to preserving the structural integrity of bonded joints. In addition, selecting the suitable welding criteria, such as voltage, present, and take a trip speed, can help minimize the risk of porosity formation. By integrating these avoidance techniques into welding techniques, the occurrence of porosity can be dramatically lowered, leading to more powerful and more dependable welded joints.
Relevance of Correct Protecting
Appropriate protecting in welding plays a crucial function in avoiding atmospheric contamination and making certain the integrity of welded joints. Shielding gases, such as argon, helium, or a blend of both, are generally used to secure the weld pool from reacting with aspects airborne like oxygen and nitrogen. When these reactive elements enter call with the hot weld pool, they can trigger porosity, leading to weak welds with reduced mechanical buildings.

Poor shielding can lead to various flaws like porosity, spatter, and oxidation, compromising the structural stability of the welded joint. Adhering to proper protecting techniques is important to produce top quality welds with minimal problems and make certain the longevity and dependability of the welded components.
Monitoring and Control Techniques
Just how can welders successfully keep track of and control the welding procedure to make certain optimum outcomes and prevent defects like porosity? By continually checking these variables, welders can recognize inconsistencies from the ideal problems and make immediate modifications to protect against porosity formation.

Furthermore, carrying out correct training programs for welders is necessary for keeping an eye on and controlling the welding process efficiently. What is Porosity. Enlightening welders on the significance of maintaining regular specifications, such as appropriate gas click shielding and travel rate, can help protect against porosity problems. Routine analyses and certifications can additionally make sure that welders are efficient in tracking and managing welding procedures
In addition, using automated welding systems can improve surveillance and control abilities. These systems can precisely regulate welding specifications, minimizing the chance of human error and ensuring regular weld top quality. By combining sophisticated surveillance innovations, training programs, and automated systems, welders can efficiently keep track of and manage the welding process to decrease porosity defects and attain premium welds.
Final Thought
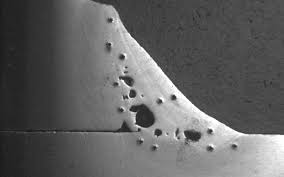